Making cast-resin 3D printer parts
August 13, 2011
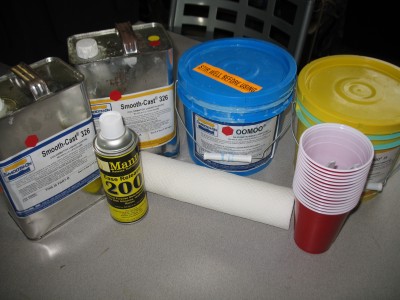
I think I’ve alluded to the fact that I spent part of this summer making cast-resin 3D printer parts. In this entry, I’ll talk about the process for doing that. What’s interesting about this process is that you can also use it for making copies of pretty much any other object as well, as long as there are no severe overhangs in the objects you’re dealing with (more than that later).
Why would you want to make cast-resin 3D printer parts? After all, the RepRap project is set up so that you can print these particular parts on your printer, which should make casting unnecessary. And actually, casting is sort of philosophically in conflict with the RepRap project, since the whole idea of the project is for these printers to reproduce themselves; casting decidedly does not fit with this.
On the other hand, it’s really easy _if you can do it right _(or if you aren’t too hung up on quality). You can make a lot of parts this way, too, quickly and cheaply.
It also, depending on the source parts you’re using, and how proficient you are with a drill press, can produce much higher-quality parts than those you’d get by printing - and better-looking ones, too.
So, it’s very useful to know how to do. But there are significant problems with the process that prevent me from recommending it wholeheartedly, which I’ll talk about at the end of this post.
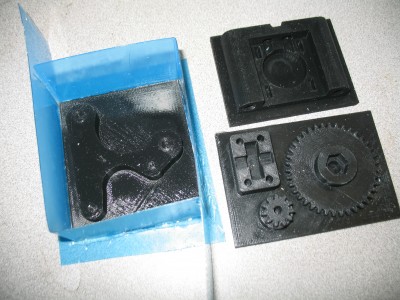
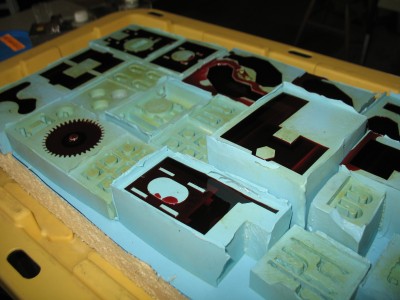
Making the master molds
** **The first step is to acquire mold casting material. We’ll use this to create a set of “master molds” which are actually spatial negatives of our objects. We’ll then be able to pour resin into these molds to create our copies.
For this project, we used Oomoo 25, but you can probably use Oomoo 30 or anything else that’s similar. I’ll refer to these molds as “master molds” or “silicone molds” throughout the rest of the post, but you don’t have to use silicone if you’d rather use something else. I may also refer to the material for this as “silicone material”.
You also, of course, need an initial set of printed parts that you are copying. We had the good fortune to acquire some parts that were printed on a Stratasys machine (i.e. professionally printed). I tried this process with some parts that had been printed on a well-functioning RepRap, and that worked pretty well also. But you will definitely end up with an exact copy, with any imperfections completely intact.
We used PETG plastic, which creases easily, to form boxes around each part. Once that’s hot-glued together, and the part glued into the box, you end up with a positive mold that you can then pour your silicone material into. And that’s the next step - you mix and pour your liquid molding material into your molds, and wait for it to dry. Don’t forget to first spray the molds with mold release; that’s very important (though in a pinch I was successful using olive oil).
I would strongly recommend casting master molds such that you have an entire set - for example, don’t try to cut corners by only making one master mold for the 3 endstop holders. If you have to reuse even one mold to get a complete set of parts, you dramatically increase the amount of time it takes to pour a resin set, since you have to wait for the first set to setup, demold it, and then pour another set.
If you have the cash, you might even want to mold all the parts as a single, giant mold. That would make things really fast, though you might use a lot more silicone mold material since some parts are much taller than others.
Making the cast-resin parts
Once you’re done mixing up your flexible mold material, pouring it, and setting it, you have your master molds. You can now easily get complete sets of 3D printer parts by applying mold release, mixing up some resin, and pouring it in. You can also add colored pigments to your resin to make frankly awesome translucent colored sets.
It’s not that cheap per set - we estimated that at the resin quantities we were buying, sets cost $20 each. Certainly not bad, but recall that each set needs to be deflashed and drilled before it can be used, which takes an hour or so each time. There’s also the time commitment of pouring the resin and waiting for it to set. Obviously you can do something else while you wait, but it isn’t a trivial time commitment. Neither is printing the sets, I suppose, but that requires a lot less attention.
I used my homemade vacuum former to create attractive packaging for these sets once they were complete.
Problems, some with possible solutions
As much as I enjoyed learning this process (and indeed trying to start a business with it), there are lots and lots of problems with what I’ve outlined here. Overall, I think it’s probably useful if you want to make some parts for yourself and your friends - or to do other object copying - but I’m not sure it’s ultimately scalable.
**Acquiring high-quality original parts is expensive or time-consuming. **
If you can get a friend with a professional 3D printer to print them for you, that’s great, but if you have to go to Shapeways or another printer, you’re looking at hundreds or thousands of dollars for a set of high-quality parts.
You can also print them yourself of course, but they have to be pretty high-quality, and you need to get an entire set printed. Also, we recommend that all the originals be printed on relatively thick rafts so that they can easily be glued down for your initial mold creation.
The master molds that are produced may not stand up to repeated use.
There are several parts that have significant overhangs or other protrusions that are very hard on silicone molds. So you will, in all likelihood, quickly break a small, key part of one of your molds (for example, a nub that corresponds to a screwhole in your original parts).
At that point, you will have to make that silicone mold over again. Huge pain, and not cheap after a while. We thought that our molds would last for 25 - 50 sets, it turned out that several parts could only take the deformation stress of demolding 10 sets or so.
One solution to this would be to get master mold material with less flexibility. This means more durability, though it may be harder to get your parts out. You could also try sanding your parts to reduce the angles at which smaller parts protrude, but this is not that easy to do.
A related problem (because of the viscosity of the silicone mold material) is that it’s very easy to leave bubbles in your master molds. If the bubbles are in your master molds, you end up with _extra material in each set you pour. _This can be a totally minor issue if the extra material is somewhere harmless, or a fatal flaw in many other cases.
Also, if your molds are set up such that any of them have thin walls, you may find that these walls sag as the silicone ages. This might not matter at all, or it might require a re-mold or reinforcement.
There’s lots of manual post-processing that may have to be done.
All parts have to be deflashed, unless you learn to pour exactly the right quantity of resin in each mold. It’s definitely possible to get better at this, but it will still take you at least a few minutes for each set.
If you overpour significantly, you will need to get out your saw because the flash will be too thick to snip off.
One solution to this would be to include small channels in between master molds that let any resin overflow go straight into another part.
If you want to get really fancy, you could build molds with _lids _so that overpour is impossible. (Small holes in the top allow pouring resin in and escape of overpour). While you would be guaranteeing yourself perfect parts every time, creating these lids would be complicated.
Your parts also need to be drilled with a drill press, unlike printed parts. This is pretty difficult, actually. Let’s assume you own a drill press and are a skilled user (these are not trivial assumptions).
You still have to track down the correct bit sizes, which can be quite difficult especially in the US.
You also have to drill certain parts with fairly high levels of precision to ensure they will actually function as intended; this is not an easy task in cases where the holes may need to be an inch or two long.
In some cases, you may not be able to tell you’ve made a mistake until you go to install the part.
Many of the resulting parts (such as the clamps) are also very easy to break when you’re drilling them. In which case, you’ve got to get all your supplies out again, respray your molds, and then wait for your new part to set before trying again.
There’s a technique to doing the pouring.
If you pour too quickly, you end up with lots of bubbles, which look strange. (Bubbles do look cool in small quantities).
If you pour too slowly, you may not finish pouring before your resin starts to set up.
Luckily, you don’t have to pour all the resin in one shot. That is to say, if you run out in the middle of pouring a particular part, you can just pour more resin on it later and it will look fine.
There are questions about what resin is right to use. We used Smooth-On 326, but it’s not entirely clear if the heat tolerance of this resin is high enough for use in the extruder block. Other resins might be more suitable.
You should still really print the PLA bushings, since resin doesn’t slide as well on the smooth rods.
Conclusion
As I said, this was a really interesting process to learn. But, as you can see from the above, resin casting is quite difficult, particularly if you want to produce high-quality parts.
If you have some time and interesting in doing this, or your printer isn’t working well enough to print parts for your friends, I’d say give this a shot. However, I’m not sure if this is a viable part production strategy overall.